- Polypropylene spinning machine
- Polypropylene FDY equipment
- Polyester POY spinning machine
- Polyamide FDY common and high strength equipment
- Polyester FDY equipment
- Polyester high strength equipment
- polyester、Polyamide、 Polypropylene BCF equipment
- Small spinning machine
- All kinds of spinning special parts
- Struggle writes the spring and autumn, diligence reveals the charm of craftsmanship | Fubang Machinery wishes everyone a happy May Day!
- The China (Shishi) International Textile and Apparel Expo and the National Fashion Textile and Apparel Supply Chain Exhibition kicked off
- Focus on six core modules to unlock new driving forces for the upgrading of the recycled fiber industry chain
- Argentina has lifted anti-dumping duties. The Textile Association has taken measures to break the deadlock and help foreign trade enterprises navigate the international market!
- Cotton textile industry fifteen five development guidance seminar was held in Anqing
- Explore the spinning machine: four functional areas, open the secret door of fiber production
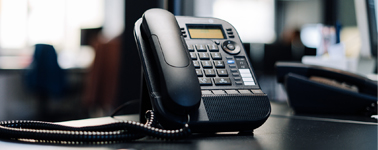
- Contact:Mr. Huang Guofu
- Cel:0086-13901505556
- Fax:0086-519-83341119
- Email:czfb5556@126.com
- Add:No. 288-8 ChangLi Rd, Huangli Town, Changzhou, JS PRV.
Textile News Since late September, due to the dual control of energy consumption, nylon manufacturers have reduced production due to power cuts, under-operated, coupled with strong support from the raw material end, and inventories have declined. Although the price fell slightly at the beginning of this week, the overall price of nylon is still running at a high level. Nylon high-position nylon grey cloth inventory is tight As of October 25, the quotation of nylon filament DTY in Jiangsu area was 22,050 yuan/ton, an increase of about 850 yuan/ton from the end of September, an increase of 4.0%; the quotation of nylon POY was 19450 yuan/ton, a decrease of 50 yuan/ton from last week , Compared with the end of September the price rose 700 yuan / ton, an increase of 3.73%; the price of nylon FDY reported 20,800 yuan / ton, compared with the end of September price rose 1,050 yuan / ton, an increase of 5.3%. From the perspective of price trends, the domestic nylon fabric market continues to operate at a high level. Under the influence of the dual control policy, the nylon industry has not been spared, and the operating rate of nylon-related companies will be restricted to a certain extent. Nylon manufacturers in Jiangsu area continued to stop production or partly stopped production, and inventory was further reduced. The impact of the power curtailment policy continues In the recent period, the "power rationing and work stoppage wave" has swept more than 10 provinces across the country, and news related to "power rationing" has been on hot search several times. "In previous years, there have been power cuts during peak power consumption, but the current situation is unprecedented." With the implementation of measures such as dual energy consumption control and power curtailment, the suspension of production by textile companies has spread to many regions across the country. The relevant monitoring platform shows that at present, the operating rate of bombing in Jiangsu and Zhejiang has dropped from more than 80% before the Mid-Autumn Festival to about 60%, and the operating rate of looms has dropped from about 60% to about 40%. Industry experts predict that the impact of restricted power outages in the textile industry may continue until the end of the year. Orders of companies with limited capacity will have an impact. In recent days, the issue of tight power supply has temporarily become the focus of the textile industry. A person in charge of Shaoxing Keqiao Fabrics Enterprise who did not want to be named told the reporter of "China Textile News" that Keqiao has issued a notice so far that the temporary power cut will continue until December this year. "But I speculate that time will continue, and energy consumption control will become a long-term measure, at least until next spring." In Jiangsu Province, textile companies are also affected by the dual control of energy consumption. An energy consumption reduction control plan issued by Jiangsu Province in mid-September shows that enterprises are required to limit production according to grades. All printing and dyeing enterprises restricted production in accordance with the measures of "opening two and stopping two", divided into two batches, and produced in rotation. How do textile companies save themselves It is understood that the impact of the power curtailment policy continued in the last two months of the year end. The situation of double limits will become more severe, and the operating rate of chemical fiber enterprises will also face a continuously low situation. Under the rapid increase in costs, textile and chemical fiber companies can only choose to increase prices to pass the pressure on to the downstream and "self-help". Since October, the price increase of nylon companies has never stopped. Upstream raw material cost support Since October, another reason for the continuous increase in domestic nylon prices is the strong support of upstream raw material costs. In terms of upstream caprolactam, the current raw material pure benzene fluctuates and rises, and the cost side support is acceptable. The supply side was tight, and caprolactam oscillated at a high level after rising. Downstream on-demand procurement, enterprises start low. The end demand was affected by the environmental protection policy and did not reach the expected effect of the peak season, and the centralized replenishment market weakened. The market fundamentals are still stable, and it is expected that caprolactam prices may remain stable in the short term. Downstream market demand In October, the traditional peak season came, and the demand for nylon spinning was on the rise. With insufficient production power, most companies preferred to consume inventory in factories and cloth merchants. The inventory of conventional grey fabrics was under significant early stage pressure, but with the advancement of the production restriction time , The rapid decline of textile inventory, so that the demand on the market is greater than the supply. Considering that the impact of power curtailment will continue, downstream textile and weaving enterprises will be more difficult to increase the operating rate, or they will maintain the current level of operation. The start of the company is still at a low level. However, the increase in the number of orders has caused the company's demand for nylon to increase. Most companies Purchasing nylon raw materials with a "buy up" mentality. Raw materials are in short supply and prices rise Due to limited production capacity, since September, the term "tight supply" has been around textile people's ears. The prices of some textile raw materials have risen due to the stimulation of production restrictions and short supply. The prices have hit a record high. On October 15th, China’s main cotton futures contract was once again closed on the daily limit, with a single-day increase of 1,570 yuan/ton, and the current price of 22,855 yuan/ton, rewriting the price record since 2012. At the beginning of the year, the cotton price was still 14,000 yuan. /Ton. On October 18, the ex-factory price of Disperse Black ECT300% by many dye manufacturers has risen to 42 yuan/kg, and the prices of other products have also been raised simultaneously. In mid-September, the price of scattered black ECT300% was only 27 yuan/kg. "Because of the substantial increase in the ex-factory price of dyestuffs, some dealers even appeared to cover their goods and reluctant to sell them at the end of September." said Jun Fang, director of the media department of Shanghai Qicaiyun E-commerce Co., Ltd. Raw materials are priced at one price per day, and it is even more normal for manufacturers to seal their trays. The raw materials are in desperate situation, which has triggered the "domino" effect of "price increase-out of stock-price increase" in the textile industry, which has brought a significant impact on the entire industrial chain. "The impact on us is the increase in dyeing fees. During the '11' holiday, we received two price increase letters from dyeing factories, which ranged from about 10% to 20%." Jin Huangen said. It is understood that recently, some printing and dyeing factories in Zhejiang, Guangdong, and Jiangsu have issued notices on the adjustment of dyeing fees, and the dyeing category has been increased by 300 to 1,000 yuan/ton. On October 15, some printing and dyeing companies issued a price adjustment letter again, increasing the dyeing fee by 500 yuan/ton; if the generator is used for power supply, it will increase by 1,000 yuan/ton. Jin Huangen said frankly: "We can also understand the price increase of the dyeing factory's products, as long as the construction period can be guaranteed, everything will be fine." Golden nine silver ten is a level Wu Wei said that in addition to limited production capacity, the rapid increase in upstream cotton prices has also caught companies by surprise. "A series of issues related to customer orders and later stocking make the company's production passive." Undoubtedly, the prices of textile raw materials have risen sharply recently, and the upstream and downstream enterprises in the industrial chain can be described as mixed. Especially the industries in the middle reaches of the industry, such as fabric printing and dyeing, are facing greater crises and risks. The number of bankrupt, closed, and integrated companies can be seen. Survival of the fittest and overall improvement is the goal. Even so, the heads of many textile companies still understand the dual control of energy consumption. According to industry insiders, on the whole, it is necessary to fully implement the requirements for dual control of energy consumption and orderly use of electricity, but also to eliminate formalisms such as "one size fits all" and "expansion" and create a brand new energy supply. The ability layout is unfolding. Disclaimer: This article is compiled from the Internet, and the copyright belongs to the original author; if there is any infringement, please inform in time and delete it after verification.
- Struggle writes the spring and autumn, diligence reveals the charm of craftsmanship | Fuba
- The China (Shishi) International Textile and Apparel Expo and the National Fashion Textile
- Focus on six core modules to unlock new driving forces for the upgrading of the recycled f
- Argentina has lifted anti-dumping duties. The Textile Association has taken measures to br
- Cotton textile industry fifteen five development guidance seminar was held in Anqing
- Explore the spinning machine: four functional areas, open the secret door of fiber product
- Manager must read | say goodbye to control management, release the potential of employees,
- Empower the traditional garment industry with digital technology
- Fubon Chemical fiber Polyester industrial silk spinning and drawing machine equipment: the
- Textile information | Industry empowerment, when calligraphy meets fabric, Keqiao textile'