- Polypropylene spinning machine
- Polypropylene FDY equipment
- Polyester POY spinning machine
- Polyamide FDY common and high strength equipment
- Polyester FDY equipment
- Polyester high strength equipment
- polyester、Polyamide、 Polypropylene BCF equipment
- Small spinning machine
- All kinds of spinning special parts
- Struggle writes the spring and autumn, diligence reveals the charm of craftsmanship | Fubang Machinery wishes everyone a happy May Day!
- The China (Shishi) International Textile and Apparel Expo and the National Fashion Textile and Apparel Supply Chain Exhibition kicked off
- Focus on six core modules to unlock new driving forces for the upgrading of the recycled fiber industry chain
- Argentina has lifted anti-dumping duties. The Textile Association has taken measures to break the deadlock and help foreign trade enterprises navigate the international market!
- Cotton textile industry fifteen five development guidance seminar was held in Anqing
- Explore the spinning machine: four functional areas, open the secret door of fiber production
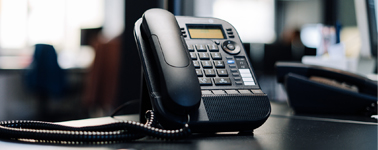
- Contact:Mr. Huang Guofu
- Cel:0086-13901505556
- Fax:0086-519-83341119
- Email:czfb5556@126.com
- Add:No. 288-8 ChangLi Rd, Huangli Town, Changzhou, JS PRV.
At present, the spinning equipment of Chinese enterprises is becoming more and more advanced, but the quality of many enterprises is difficult to improve. There are many reasons. A brief analysis of the quality problems is mainly related to raw materials, equipment, technology, air conditioning, management, etc., but Inadequate simple management is also an important reason why the quality is difficult to achieve the desired quality. This article simply analyzes the problems in daily management and puts forward suggestions for rectification, which have certain reference value for improving yarn quality and reducing yarn defects.
In terms of raw cotton management, many companies currently do not have enough reserves, resulting in inadequate batches of raw cotton and excessively large batches, resulting in yarn color problems. The amount of cotton reserves must match the amount of production used, so that batches can be received normally. At the same time, it is necessary to strictly control the raw cotton purchase. Some raw cotton is processed, although it feels better, but it has very poor spinnability. Table 1 is the AFIS test data of two batches of real estate cotton used by a domestic cotton spinning factory. The two cotton samples have no obvious difference in hand feel, but it can be seen from the AFIS test data that there are obvious differences in quality indicators. Although the purchase price of sample 2 may be lower than that of sample 1, its high lint rate and high neps will directly affect the quality of yarn.
The outer side of the raw cotton is mildewed or the incidental debris is not cleaned up. Although most of the blow-up and carding units are now equipped with complete foreign fiber removal machines and trash removal systems, they cannot eliminate such dirty flowers and impurities 100%.
Some enterprises do not manage the use of reeling in place, which affects the quality of the finished yarn. The general principle for the use of re-spending in spinning mills is: for ordinary ring carded yarn, the recycle ratio generally does not exceed 5%, and the recycle of combed yarn The use ratio should not exceed 2.5%, and in the process of use, pay attention to the packing density and placement of the return sliver. The packing density of the return sliver should be close to or consistent with the density of the bale. The return sliver must be torn off before returning. It is recommended that the length of the tear is less than 30cm. However, some companies cannot strictly limit the actual use process, and control the amount of recycling according to the amount of recycling generated, and how much is used, resulting in inconsistent recycling ratios between disks, and even the quality of recycling is difficult to guarantee, such as recycling. It contains a lot of cords, and the return sliver is not broken, which has a great impact on the quality of the yarn.
One of the reasons for the lack of ingredients to grab cotton is the inconsistent height of the pack. Now the domestic Xinjiang cotton, especially the northern Xinjiang cotton and southern Xinjiang cotton, the regain of raw cotton is very different. The maximum regain of raw cotton can reach more than 10%, and the minimum is less than 6%. This causes serious inconsistency in the degree of bale increase after raw cotton is discharged. Afterwards, the production was started without flat bales, resulting in a lack of ingredients to catch cotton. Another reason is that the recycled recycles and slivers are not packaged, and are scattered directly in the overlock, resulting in a lack of ingredients and spinning.
Raw cotton management is the first step in quality management. These problems in the management and use of raw cotton are important issues to be solved in quality management.
- Struggle writes the spring and autumn, diligence reveals the charm of craftsmanship | Fuba
- The China (Shishi) International Textile and Apparel Expo and the National Fashion Textile
- Focus on six core modules to unlock new driving forces for the upgrading of the recycled f
- Argentina has lifted anti-dumping duties. The Textile Association has taken measures to br
- Cotton textile industry fifteen five development guidance seminar was held in Anqing
- Explore the spinning machine: four functional areas, open the secret door of fiber product
- Manager must read | say goodbye to control management, release the potential of employees,
- Empower the traditional garment industry with digital technology
- Fubon Chemical fiber Polyester industrial silk spinning and drawing machine equipment: the
- Textile information | Industry empowerment, when calligraphy meets fabric, Keqiao textile'