- Polypropylene spinning machine
- Polypropylene FDY equipment
- Polyester POY spinning machine
- Polyamide FDY common and high strength equipment
- Polyester FDY equipment
- Polyester high strength equipment
- polyester、Polyamide、 Polypropylene BCF equipment
- Small spinning machine
- All kinds of spinning special parts
- Management Skills: The combination of firmness and flexibility is not enough. What management requires is the art of balancing firmness when necessary and softness when appropriate!
- The national key and provincial key joint laboratories of the textile industry were launched in Shengze
- It turns out that the filament spun by the polypropylene FDY spinning machine has so many uses
- Textile News: AI and Intangible Cultural Heritage Dance Together: How Does Chinese Craftsmanship Amaze the World Stage?
- The 2025 Wuhan Shishang Industry Summit sets sail anew
- How does a polypropylene spinning machine reshape the quality genes of polypropylene filament?
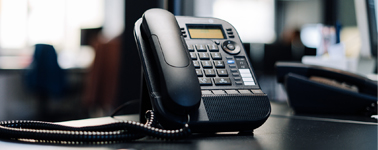
- Contact:Mr. Huang Guofu
- Cel:0086-13901505556
- Fax:0086-519-83341119
- Email:czfb5556@126.com
- Add:No. 288-8 ChangLi Rd, Huangli Town, Changzhou, JS PRV.
What are the suitable heating methods for polypropylene spinning machines? The heating of the polypropylene spinning machine requires the use of an electromagnetic heater. The main component of the machine is a heat roller, which can heat to a certain temperature and run at high speed.
The size of the heat roller is different. Generally, the diameter is Φ160 Φ180 Φ190 Φ210 Φ220. Length of hot roller: 200-450mm, speed range: 750-5500m / min, surface temperature of guide wire disk: ≤240 ℃ -140 ℃, surface treatment of hot roller: hard chromium plating, ceramic plating
The current heating method of the heat roller is industrial frequency induction heating. Its disadvantage is that the heating coil is easily damaged. The terrible thing is that it is easy to heat the center shaft of the motor and burn the motor. However, the newly-developed all-digital is applied to the heating of polypropylene roller spinning machine with high efficiency and energy saving, which effectively solves the disadvantages of traditional heating and greatly reduces the cost. Its main advantages are:
1. The surface temperature of the working area of the heat roller can be made uniform, which can meet the requirements of different industrial and civilian filament FDY spinning processes.
2. The surface temperature of the working area of the heat roller is heated up rapidly, the energy saving is obvious, and the efficiency is greatly improved.
3. After using the electromagnetic heater, the rotating shaft of the heat roller motor will not damage the motor due to induction heating.
4. The coil of the electromagnetic heater will not be damaged, reducing maintenance trouble and cost.
5. This equipment has a complete system, simple structure, stable and reliable operation at high temperatures, can meet the requirements of different fiber FDY spinning processes, and is an economical and reasonable choice for polypropylene spinning machines.
- Management Skills: The combination of firmness and flexibility is not enough. What managem
- The national key and provincial key joint laboratories of the textile industry were launch
- It turns out that the filament spun by the polypropylene FDY spinning machine has so many
- Textile News: AI and Intangible Cultural Heritage Dance Together: How Does Chinese Craftsm
- The 2025 Wuhan Shishang Industry Summit sets sail anew
- How does a polypropylene spinning machine reshape the quality genes of polypropylene filam
- How to scientifically evaluate the working efficiency of a polypropylene spinning machine
- The Battle Song of Longcheng | Beyond Victory and Defeat, the spirit of Changzhou burns Fo
- @All partners: The Summer Solstice has arrived. Fubang Machinery takes you to unlock the S
- The 2025 Greater Bay Area International Textile Yarn Expo was held