- Polypropylene spinning machine
- Polypropylene FDY equipment
- Polyester POY spinning machine
- Polyamide FDY common and high strength equipment
- Polyester FDY equipment
- Polyester high strength equipment
- polyester、Polyamide、 Polypropylene BCF equipment
- Small spinning machine
- All kinds of spinning special parts
- The Battle Song of Longcheng | Beyond Victory and Defeat, the spirit of Changzhou burns Forever! Fubang Chemical Fiber Machinery is cheering for the Changzhou team of the Scottish Premier League!
- How to scientifically evaluate the working efficiency of a polypropylene spinning machine
- @All partners: The Summer Solstice has arrived. Fubang Machinery takes you to unlock the Summer Solstice health guide and start a healthy summer!
- The 2025 Greater Bay Area International Textile Yarn Expo was held
- Detailed Explanation of the Inspection Standards for Polypropylene Spinning Machine Equipment: The Key to Ensuring Efficient Production
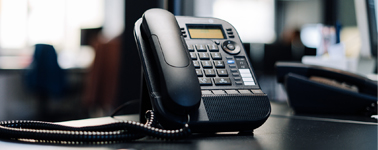
- Contact:Mr. Huang Guofu
- Cel:0086-13901505556
- Fax:0086-519-83341119
- Email:czfb5556@126.com
- Add:No. 288-8 ChangLi Rd, Huangli Town, Changzhou, JS PRV.
Textile production is a labor-intensive industry with many production personnel, many machines and equipment, and there are adverse environments such as dust and noise. Textile raw materials are flammable and cause a high probability of fire.
On March 15, 1987, a large linen dust explosion occurred in the Harbin Flax Factory, killing 58 people and injuring 177 people, shocking the country.
At 7:34 on August 2, 2014, a special aluminum dust explosion occurred in the polishing second workshop of Kunshan Zhongrong Metal Products Co., Ltd. of Kunshan Economic and Technological Development Zone in Suzhou City, causing 75 deaths and 185 injuries on the same day.
These accidents have sounded the alarm for safety production for textile companies.
Dust explosion conditions
First, there must be a certain concentration of dust. The stoichiometric concentration unit used for dust explosion is different from gas explosion. The gas explosion is expressed by volume percentage, and the dust concentration is expressed by the mass of dust particles contained per unit volume. The unit is g/ M3 or mg/L.
Second, to have a certain oxygen content, a certain oxygen content is the basis for the dust to burn.
Third, there must be enough ignition sources. The minimum ignition energy required for dust explosion is one to two orders of magnitude larger than that of gas explosion. The minimum ignition energy of most dust clouds is in the range of 5mJ to 50mJ.
Fourth, the dust must be in a suspended state, that is, a dust cloud state, which can increase the gas-solid contact area and speed up the reaction.
Fifth, the dust cloud should be in a relatively closed space, and the pressure and temperature can rise sharply and then explode.
Daily protective measures
In order to prevent the occurrence of explosion accidents, textile mills should focus on the following aspects:
1. The pre-spinning workshop, especially the carding, must be equipped with dust removal equipment or devices. According to the relevant requirements of the state, the dust-removal form shall not adopt the positive pressure mode.
2. Dust removal equipment should use combined dust removal equipment that does not produce sparks, continuous filtration, dust collection, compaction and removal. It is strictly forbidden to use sedimentation type dust removal.
3. The air dust concentration in the spinning workshop should be controlled below 3mg/m3.
4. Dust rooms should be ventilated and not closed.
5. Dust room should pay attention to clean and hygienic management, and waste cotton should be removed in time to avoid accumulation.
6. The dust equipment must be safely up to standard, equipped with an explosion-proof motor and a safety relief device; the dust chamber must be equipped with an explosion-proof switch and explosion-proof lighting.
7. Equipments that are prone to dust explosions are dust collectors, dust collectors, wind conveyors, trenches, etc. Therefore, the spinning and dedusting should not use the trench type as much as possible. Let alone the construction difficulty. Only dust deposition is an unsafe factor.
8. Always check electrical switches and wiring to standardize safe power usage.
9. The fire detection device should be equipped in the cleaning process, the dust filter pipe, the entrance of the dust filter, etc., and require special personnel to maintain and manage.
10. There must be fire separation between the areas of front spinning, spinning, and post-processing. It is best to install fire doors. It is very unsafe for some companies to set together raw materials and cleaning processes.
11. The necessary fire exits and evacuation passages must be available and must not be blocked.
12. Fire extinguishers, talc buckets, fire hydrants and other equipment must be in good condition and can be used correctly.
13. To implement open fire operations such as electric welding gas cutting, there must be an approval system, and there must be responsible persons and guardians.
14. Improve the fire prevention system and strictly enforce it, and have a fire plan. Conditional companies set up voluntary fire brigades and often practice.
15. Enterprise management personnel, especially business owners (bosses) must pay attention to fire safety, and all employees must have a strong sense of security.
Textile enterprises, especially spinning mills, are the top priority of all fires. Preventing problems before they happen, I hope that enterprises can develop in peace and not regret it because of luck.
Changzhou Fubon Chemical Fiber Machinery Factory mainly produces: polyester industrial yarn spinning combined machine, polyester POY spinning machine, polypropylene FDY spinning machine, polypropylene FDY production line, polypropylene FDY equipment, polypropylene FDY machinery, polyester industrial yarn spinning combined machine, Polyester FDY spinning machine, polypropylene spinning machine, polyester FDY production line, polyester FDY machine, nylon FDY spinning machine, polyester industrial yarn spinning machine.
- How to scientifically evaluate the working efficiency of a polypropylene spinning machine
- The Battle Song of Longcheng | Beyond Victory and Defeat, the spirit of Changzhou burns Fo
- @All partners: The Summer Solstice has arrived. Fubang Machinery takes you to unlock the S
- The 2025 Greater Bay Area International Textile Yarn Expo was held
- Detailed Explanation of the Inspection Standards for Polypropylene Spinning Machine Equipm
- Small samples of Changshu home textiles have driven large orders
- Entering the Polypropylene Spinning Machine: A Grand Revelation of the Four Functional Zon
- Textile News | Over 40 embroidery styles compete on the same stage, Summer Cloth embroider
- The Grain in Ear Festival inspires dreams, and the brush battles in the examination room |
- During the Dragon Boat Festival holiday, textile enterprises remained open. Which fabrics