- Polypropylene spinning machine
- Polypropylene FDY equipment
- Polyester POY spinning machine
- Polyamide FDY common and high strength equipment
- Polyester FDY equipment
- Polyester high strength equipment
- polyester、Polyamide、 Polypropylene BCF equipment
- Small spinning machine
- All kinds of spinning special parts
- Comprehensive Analysis of Core Components of polypropylene spinning machines: From Screw Extrusion to Intelligent Winding
- The 2025 Qilu Fashion Conference was held in Jinan
- The Start of Autumn has arrived, and the coolness of autumn begins. From the solar terms to production, Fubang Machinery is with you to maintain quality and enhance efficiency!
- The Academic Conference on Intelligent Manufacturing and Industrial Upgrading of China's Spinning Industry was held in Yancheng
- New Trends in the technological upgrade and industry application of polypropylene spinning machines
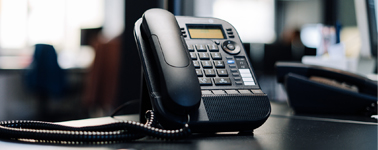
- Contact:Mr. Huang Guofu
- Cel:0086-13901505556
- Fax:0086-519-83341119
- Email:czfb5556@126.com
- Add:No. 288-8 ChangLi Rd, Huangli Town, Changzhou, JS PRV.
The polypropylene spinning machine is the core equipment in the production of polypropylene (polypropylene fiber), and its role runs through the entire production process, having a decisive impact on product quality, production efficiency and the technological development of the industry. The following are its specific roles in the polypropylene industry:
Core production functions
Melt spinning: After heating and melting polypropylene particles, they are extruded through a spinneret to form primary fibers, which is a key step in fiber forming.
Stretching and setting: By adjusting the molecular orientation and crystallinity of fibers through a multi-stage stretching system, the mechanical properties such as strength and elongation of the fibers are directly affected.
Cooling and curing: Control the cooling rate of the filament to ensure the uniformity and stability of the fiber structure.
2. Determine the product quality
Fiber fineness and uniformity: The design of the spinneret (pore size, arrangement) and process parameters (temperature, pressure) determine the fineness and uniformity of the fibers, which affects the quality of the subsequent textiles.
Mechanical property optimization: By adjusting parameters such as the stretching ratio and temperature, high-strength and low-shrinkage special polypropylene can be produced (such as industrial ropes, geotextiles, etc.).
3. Improved production efficiency
High-speed production: Modern spinning machines can reach a speed of 3,000 to 6,000 meters per minute, significantly enhancing production capacity and reducing unit costs.
Continuous operation: An integrated design that combines melting, spinning and winding reduces downtime and is suitable for large-scale production.
4. Diversified product development
Multi-functional fiber production: By modifying components (such as composite spinnerets), special fibers such as hollow, special-shaped cross-section, and ultra-fine denier can be produced, and their applications can be expanded to fields such as filter materials and medical textiles.
Differentiated process support: such as FDY (fully drawn filament), POY (pre-oriented filament), and other different process routes to meet the demands of downstream texturing, weaving, etc.
5. Contributions to energy conservation and environmental protection
Low energy consumption design: High-efficiency screw extruders and heat recovery systems are adopted to reduce energy consumption.
Reduce waste: Precise automated control reduces the rate of broken wires and waste wires, and some waste can be recycled online.
6. Driving force of technological upgrading
Intelligent transformation: Integrating online monitoring (such as ultrasonic diameter gauges) and AI process optimization systems to achieve real-time quality control.
New material compatibility: Compatible with modified polypropylene (such as antibacterial and flame-retardant masterbatches), promoting innovation in functional fibers.
7. Industrial chain impact
Upstream linkage: The performance requirements of the equipment drive the improvement of the quality standards for polypropylene chips.
Downstream expansion: The differentiated fibers produced support high-end application markets such as automotive interiors and sportswear.
Practical application cases
Geotextile production: Coarse denier fibers produced by high-strength polypropylene spinning machines are used for reinforcing highway subgrades.
Medical non-woven fabric: Ultrafine fibers produced by fine denier spinning machines (< 1 denier), used as surgical protective materials.
Summary
The polypropylene spinning machine is not only a production tool but also a carrier of technological progress in the industry. Its technological level directly determines the market competitiveness of polypropylene products and promotes the transformation from traditional packaging materials to high-tech content fields. In the future, with the development of modular design and green manufacturing technologies, their roles will be further deepened.
Changzhou Fubon Chemical Fiber Machinery Factory Technical production: Polypropylene spinning machine, polypropylene FDY spinning machine, polypropylene FDY equipment, polyester POY spinning machine, polyester POY production line, polyester POY equipment, polyester POY machinery, polyester recycled bottle FDY spinning machine, polyester FDY spinning machine, polyester FDY machinery, Spandex spinning machine, spinning special parts, polyester small Experimental machine, polypropylene small experimental machine, nylon small experimental machine.
Changzhou Fubon Chemical Fiber Machinery Factory Technical is a research and development and production of all kinds of chemical fiber machinery as the main professional manufacturing suppliers, research, development, production and sales as one, in order to meet the market demand, our factory has established a perfect chemical fiber spinning experimental base, to provide customers with good equipment and technical services. We mainly provide customers with complete sets of polyester, polypropylene, nylon, spandex and other chemical fiber complete sets of equipment, and undertake a variety of related equipment renovation projects and customized services.
- The 2025 Qilu Fashion Conference was held in Jinan
- Comprehensive Analysis of Core Components of polypropylene spinning machines: From Screw E
- The Start of Autumn has arrived, and the coolness of autumn begins. From the solar terms t
- The Academic Conference on Intelligent Manufacturing and Industrial Upgrading of China's S
- New Trends in the technological upgrade and industry application of polypropylene spinning
- National Trend Intangible Cultural Heritage + Technology Empowerment! From domestic trends
- China's yarn exports increased by 6.4% in the first six months
- Polypropylene spinning machine complete set of equipment: Empowering production with outst
- The key to team cohesion: Choosing the right leader can achieve twice the result with half
- Eight departments jointly issued the Implementation Plan for Digital Transformation of the